A Work order is an order to make one or more products. Conventionally, the work order uses a bill of materials (BOM) to create a list of materials to be issued, and a routing to make a list of operations to be performed on work centers. Work orders dictate what product need to be manufactured, what raw materials are going to be required to manufacture the product, and which work center that the product needs to pass through in the manufacturing process.
Some companies would like to create their Finished Good products with a Lot Number that is the same as the Work Order Number that created the product. Finished goods are goods that have been completed by the manufacturing process, or purchased in a completed form, but which have not yet been sold to customers.
Why we make the Lot number same as Work order number because this can make the tracing of the Lot easier. In Sage X3, there is a standard functionality of doing this.
Follow below steps for the setup:
Steps:
First make sure the Lot Management setting of product is checked as a ‘Mandatory lot’ and under the Lot Sequence field this MUST be blank as shown in below figure.
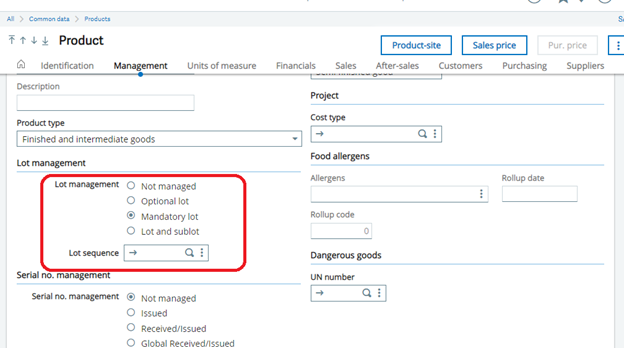
Also, Product category set up should be same as product setup, as shown in below figure.
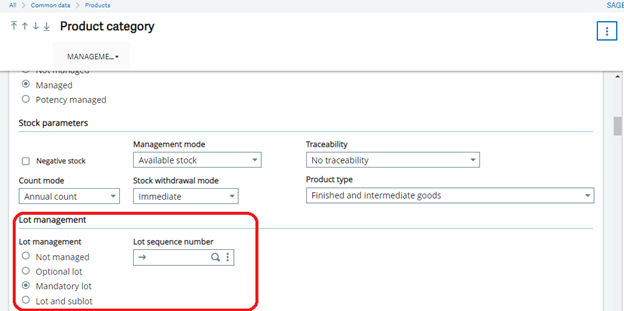
In short product and that respective product category set up should be set as defined above.
Navigate To: Common Data> Product category > Receipts Tab > Management Rules Grid
- Select Movement type as ‘Work order receipt’
- Change the value of Lot entry as a ‘Free’
- Change the value of Lot by default as a ‘Document number’
- Click on Save or OK button.
Please refer the below figure for the same.
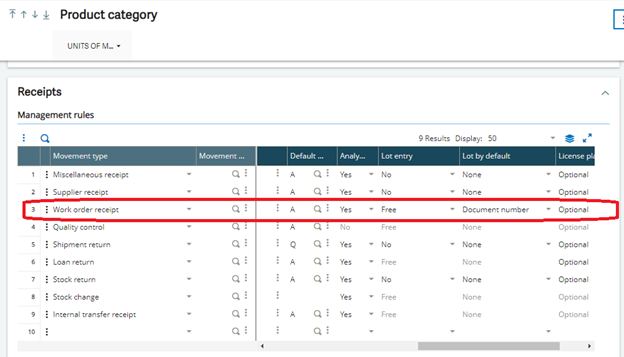
Now we have done the setup for product master and product category.
Navigate To: Set up > General parameter > Parameter values
- Select GPA chapter from left panel
- Select MIS group
- Click on the detail of MIS group from action button
- Change the value of LOTMGT as a “In release”
- Click on OK button
- Save the changes.
Refer the below screenshot for the same.
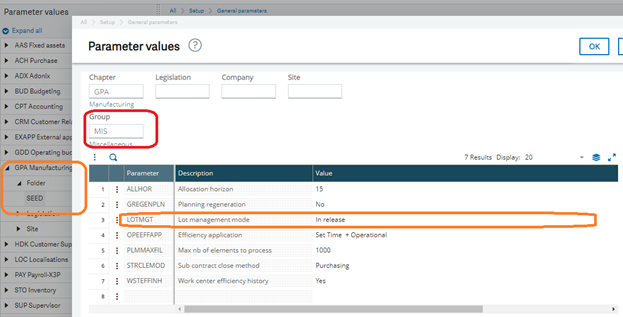
Now follow the below path for the Work order creation,
Navigate To > Manufacturing > Planning > Work order
While creating the work order transaction, keep LOT no. as blank on line level and after creation you can see LOT no. is coming same as a Work order transaction number. Refer below figure for the same.
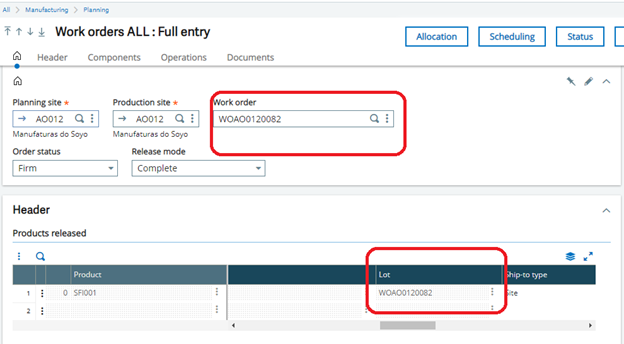
With the help of this setup you can align the Lot numbers with Work order numbers.
Hence after doing all the above steps we can able to align the same lot number with work order number.
About Us
Greytrix – a globally recognized and one of the oldest Sage Gold Development Partner is a one-stop solution provider for Sage ERP and Sage CRM organizational needs. Being acknowledged and rewarded for multi-man years of experience, we bring complete end-to-end assistance for your technical consultations, product customizations, data migration, system integrations, third-party add-on development and implementation competence.
Greytrix caters to a wide range of Sage X3, a Sage Business Cloud Solution, offerings. Our unique GUMU integrations include Sage X3 for Sage CRM, Salesforce.com, Dynamics 365 CRM and Magento eCommerce along with Implementation and Technical Support worldwide for Sage X3. Currently we are Sage X3 Implementation Partner in East Africa, Middle East, Australia, Asia, US, UK. We also offer best-in-class Sage X3 customization and development services, integrated applications such as POS | WMS | Payment Gateway | Shipping System | Business Intelligence | eCommerce and have developed add-ons such as Catch – Weight and Letter of Credit and India Legislation for Sage X3 to Sage business partners, end users and Sage PSG worldwide.
Greytrix is a recognized Sage champion ISV Partner for GUMU Sage X3 – Sage CRM integration also listed on Sage Marketplace; GUMU
integration for Sage X3 – Salesforce is a 5-star rated app listed on Salesforce AppExchange and GUMU
integration for Dynamics 365 CRM – Sage ERP listed on Microsoft AppSource.
For more information on Sage X3 Integration and Services, please contact us at x3@greytrix.com, We will like to hear from you.